Results
The aim of DREAM has been to significantly improve the performance of laser Powder Bed Fusion of titanium, aluminium, and steel components in terms of speed, costs, material use and reliability, also using a Life Cycle approach, whilst producing work pieces with controlled and significantly increased fatigue life, as well with higher strength-to-weight ratios.
The motivation for the project has been to go far beyond the state of the art in laser-based Powder Bed Fusion, by mastering of all stages of the process chain; among the numerous industrial applications, the project has focused on components for prosthetic, automotive and moulding applications to optimize the procedure respectively for titanium, aluminium and steel.
In order to upscale the results and to reach an industrial relevant level of productivity, the project has been involved in the following activities:
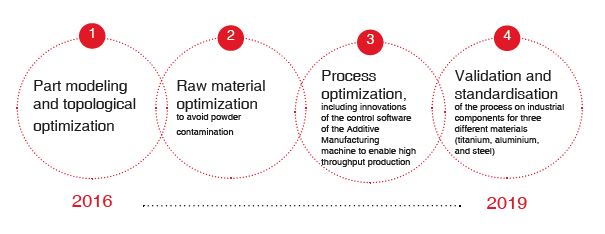
Results
1. Novel component geometry:
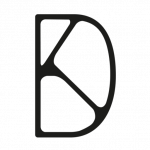
- Parts have been redesigned by applying topology optimization/design for Additive Manufacturing
- The new geometries allow for a reduction of costs (-10%), building time (10%) and part weight (-15%)
2. Use of improved and new raw materials:

- Improved quality of raw metal powders achieved through thedevelopment of procedures for cross-contamination identificationand quantification
- A novel device to remove contaminants from the raw metalpowders has been developed and tested within the productionprocess
- Novel nanostructured alloys have been developed as possiblecandidates for PBF
3. Superior process control:
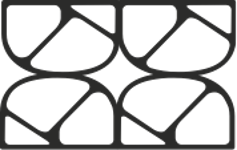
Innovations of Powder Bed Fusion machine control software have been developed, specifically:
- Better control of the effects of laser parameters on melt track instability/cooling defects
- Finer control of the heat input
- 20% augmented fatigue life
This allows for increase of productivity (+15%) and higher reliability of the AM process
Prototypes
Medium size prosthetic titanium components
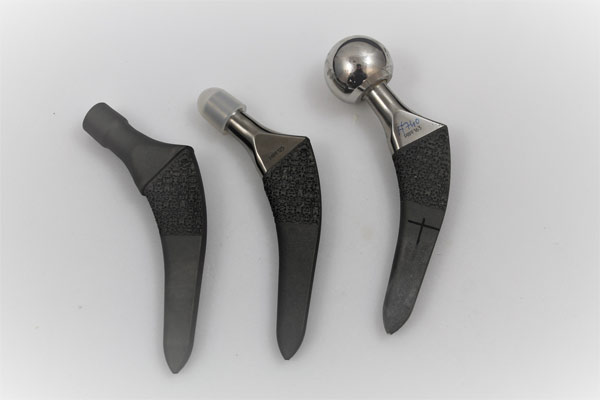
- Topology optimization obtained reducing its weight by more than 15%
- Validation of the mechanical performances
- Innovative trabecular zone for bone growth
Lightweight automotive aluminium components
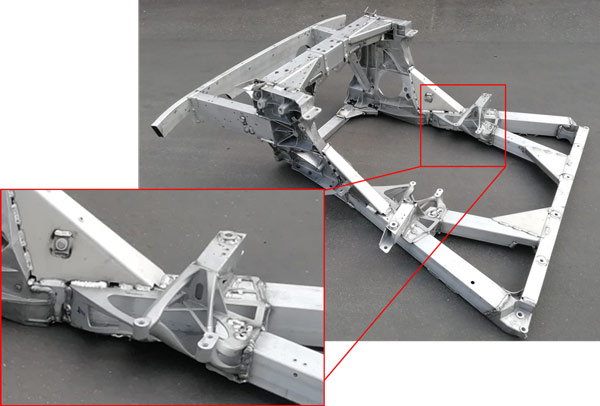
- Topology optimization carried out to drive the complete re-design of a structural spaceframe component in view of additive manufacturing technology
- New design validated among the different structural requirements. Mass saving of almost 19%
- Very good level of correlation between CAE results and physical test proven through NVH, durability and quasi-static destructive tests
Lightweight automotive aluminium components
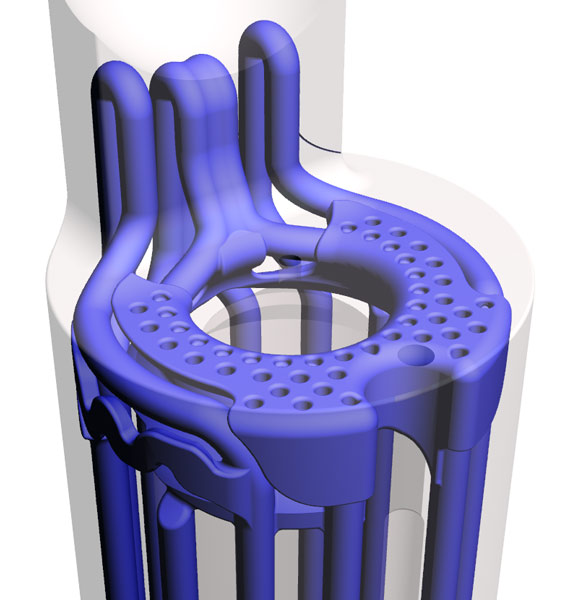
- The injected part is cooled in a more homogeneous way
- The channel penetrates deeper into the fork part
- Improved mould performance
- Developement of a new powder that improves the mechanical performances of conformal channels
About the project results
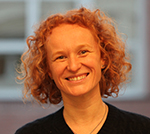
Elena Bassoli
Project Coordinator
I think that one of the main strengths of the project has been the construction of a consortium that involves all the players in the value chain, from the producer of the raw materials and the machines to the end user. This has allowed a synergistic collaboration that has allowed to exploit the enabling capacities of additive manufacturing.
The synergy between the partners has been so good and technically valid that we can think about a continuation of both the project and the relationships between the partners for other activities.
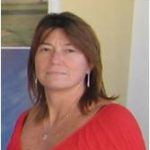
Isella Vicini
Project Manager